by Nick Drew | Fri 08 Dec 2023
Big Cat’s Prove their worth for NRW Civil & Mining
Here on the Digger Man Blog, we all love a big Cat story, and I am delighted to share this one from our friends on the team “Down Under” at Westrac Cat.
With the need for new equipment to cater for client requirements, and a preference for having a local supplier in proximity to mining operations, it was clear that Cat equipment was an excellent choice for mining services provider NRW Civil & Mining.
NRW made the decision to invest in two new mining shovels to meet some unique challenges at Karara Mining’s magnetite project in Western Australia’s Midwest region.
Located 200km south-east of Geraldton in Western Australia, Karara is the largest mining operation and the first major magnetite mine in the Midwest region. It produces a premium, high-grade concentrate product which is exported from Geraldton port.
Unlike the more commonly mined hematite, magnetite is a hard and highly abrasive ore, which meant NRW needed machines that could cope with the rigours of operating in such harsh conditions.
NRW opted for the Cat 6060 Hydraulic Mining Shovel, the next generation of a tried and true performer and the ideal face shovel for Karara Mining’s requirements.
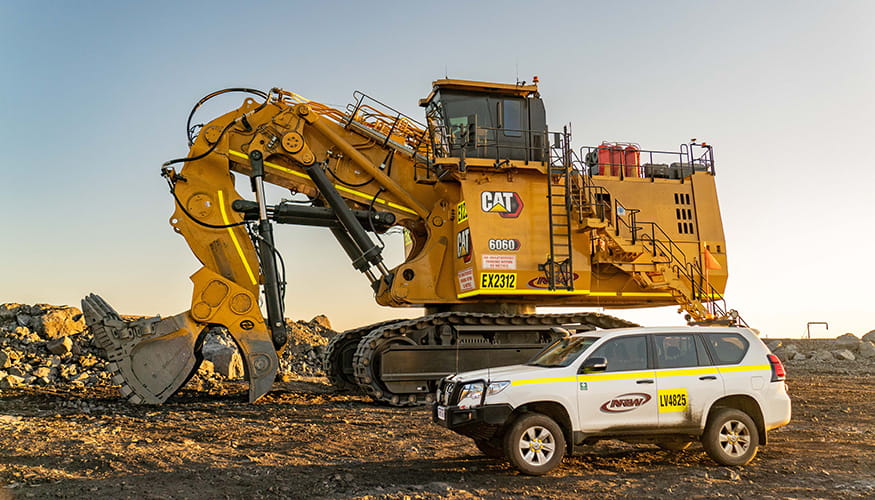
According to NRW Mining Operations Manager Adam Harper, the buying decisions for a mining contractor are very much driven by client expectations.
“We're obviously chasing safe machines, but they have to be able to perform to our clients’ expectations and do so efficiently.”
According to WesTrac Product Manager Greg Wear, the Cat 6060 is a premium Caterpillar offering when it comes to hydraulic mining shovels and has traditionally been the shovel of choice for top tier miners.
“This is the machine that we promote for highly productive loading of 240-ton (218-tonne) trucks and up,” Greg said,
“Tier one miners have had good success with that and now with NRW onboard, it shows that mining contractors are also seeing the value of the Cat 6060.”
Greg explains that the 600-tonne models have a long history, having first been released to market under previous owner Terex as the RH340 in 2004. Since being acquired by Caterpillar, the machine has been progressively “Catified” through a series of phased improvements.

“Over the past 10 years, Caterpillar has made phased improvements,” Greg said, “Phase one was a lot of quick wins that could be applied to make the machine more reliable. Phase two looked at structural changes designed to provide stronger, heavier frames and more reliability. Phase three continued that with modifications around sticks and booms, and a completely new superstructure and larger slew ring.
“Today with all the Next Generation technology, the transformation is complete with all Cat electronics and parts, and there’s been a new cab installed. Now the 6060 has the complete Caterpillar feel and functionality.
Part of the new cab design was increased visibility, allowing the operator clear views to the digging and loading areas as well as the tracks.

Somebody who has been involved through the bulk of the machine journey is Caterpillar Product Application Specialist Dirk Tegtmeier. He says the transformation of the Cat 6060 brings the same level of commonality to the large shovel that is seen across other Cat equipment.
Dirk says a key efficiency gain, thanks to the 6060 now incorporating all-Cat components and improved structures, is that service intervals and the total operating life of the machine can be extended.
“The updated Cat 3512E Engine coupled with the fuel burn saving features, thanks to new Hydraulic Optimisation, will certainly offer a longer life than with the previous version,” Dirk said.
That longevity, coupled with the added strength and Cat Enhanced Motion Control as part of the Operator Assist functionality of the Cat 6060, is important given the harsh terrain in which the new mining shovels are operating and the need to meet high production targets – with a minimum feed rate to the primary crusher of 3,500 tonnes per hour.
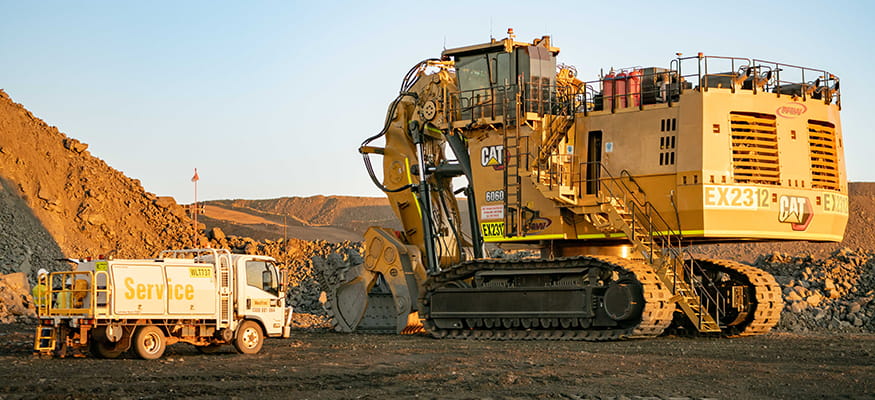
“The 6060 FS comes with an extremely productive profile that enabled us to match the client's production schedules perfectly,” Adam said.
“We also chose the Cat 793 trucks that are perfectly matched for size and passing with the 6060, so it’s a highly productive match. But we needed to ensure we had the reliability as well.”
Karara’s proximity to Geraldton and Perth – two and four-hour drives from the mine respectively – and the fact WesTrac has parts and service centres in those locations, was another key factor in NRW’s decision to go for the Cat 6060.
According to Adam, the hardness and abrasiveness of the magnetite ore means ground engagement tools can wear up to 20 times faster than in hematite mining operations, meaning regular access to spares is vital.
“The teeth on the bucket can need replacing within 24 to 70 hours, whereas in some hematite mines, it could be anywhere from 500 to 1000 hours,” Adam said.
“Having the customer service centre four hours away in Perth that runs 24/7 is crucial as it means we are able to get access to parts as needed. Also, WesTrac Geraldton being two hours away for support was really a deciding factor for us in choosing the Cat 6060s.”
Adam says NRW’s previous experience working with Cat equipment and existing relationship with WesTrac was one factor that helped win the contract with Karara Mining.
“Karara Mining Limited had a long association with Cat products, in particular the 6060 face shovels and the 793 dump trucks, and that played a big part in helping win the contract,” Adam said.
“We both have confidence in the products and that’s allowed the relationship between Karara Mining and NRW to flourish.”

With a 30-year expected life of mine at Karara, NRW expects the Cat 6060 machines to be put through their paces – and to deliver outstanding results.
Checkout the video from Westrac Cat below.
The Digger Man Blog would like to thank Westrac Cat for the material, images and video contained in this blog post.