by Nick Drew | Tue 07 Jan 2025
Going Underground
Taking a look back at one of my articles previously published in Earthmovers, un-edited and with alternative images.
Jamie Warmisham previously worked in the utilities sector for TJ Brent a once well-known sub-contracting business that used to do all the work in the South West for the local water authority. During a 5-year stint with the business Jamie gained a lot of valuable experience in the sector, travelling and undertaking jobs right across the region and sometimes further afield.
However, as is often the case, a change in senior management changed the status quo somewhat, and so Jamie (pictured above) decided it was time for a change. In 2011 he decided to set up his own Cornwall based business, Underground Solutions Ltd, along with his wife and fellow Managing Director Sam.
Working primarily in the major utilities sector the company specializes in what they describe as non-destructive digging, using the latest cutting-edge technology to excavate and reveal underground utilities in a safe manner, in particular vacuum excavation trucks, of which they are currently running six with another two expected to join the fleet next year.
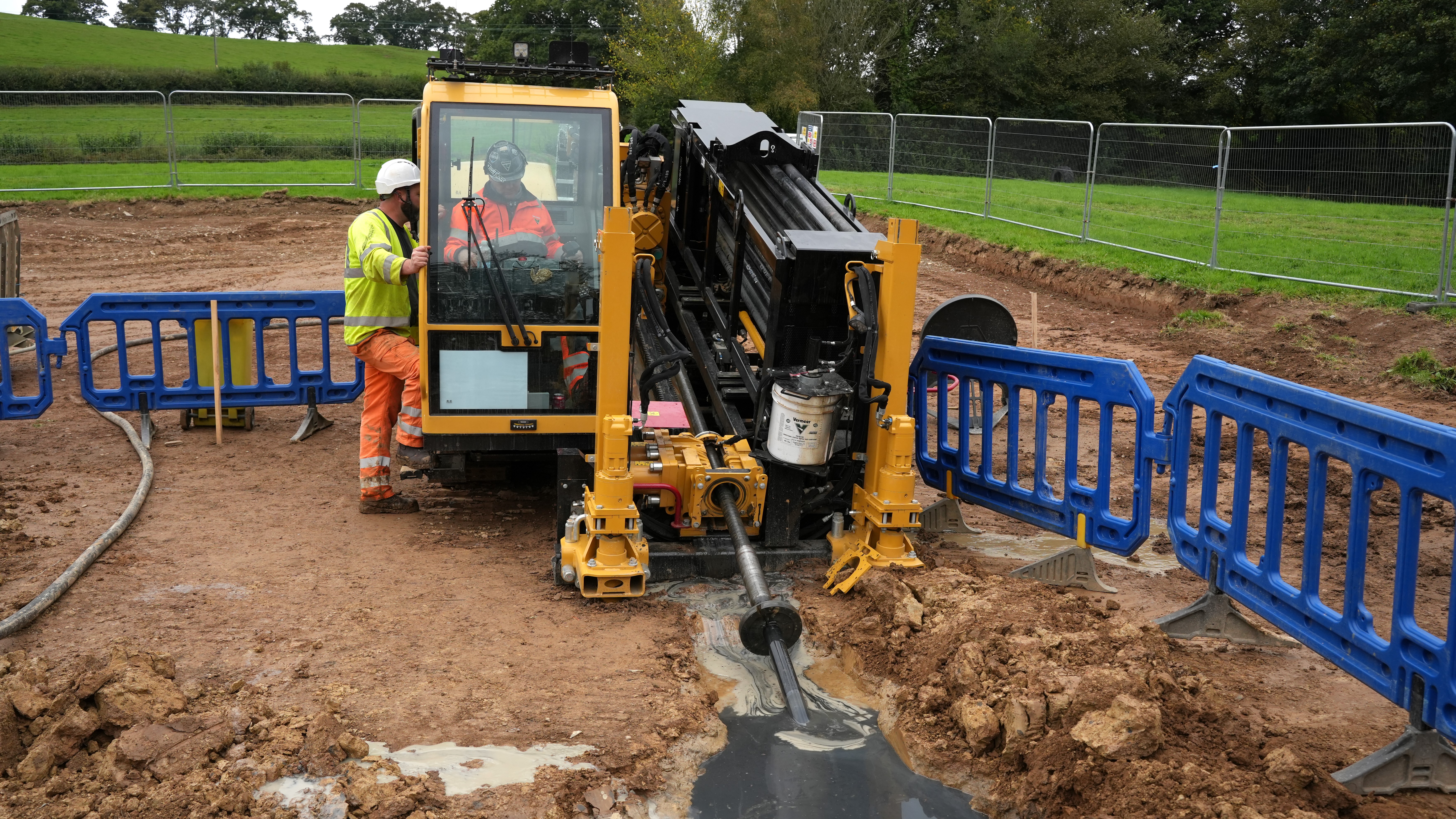
Alongside and complementing the fleet of trucks, they are running a wide variety of hydraulic excavators, ranging from 1-tonne up to 13/14-tonne, around twenty in total from Takeuchi, arguably the utility sectors favourite mini excavator, CASE, a few SANY models and a DEVELON.
Most of their work is for water, gas or electrical contractors which see’s them supplying the mini excavators as part of a two-man team. They are currently directly employing around 50 individuals all of whom have vast experience in the sector, ranging from intricate urban jobsites to massive construction projects.
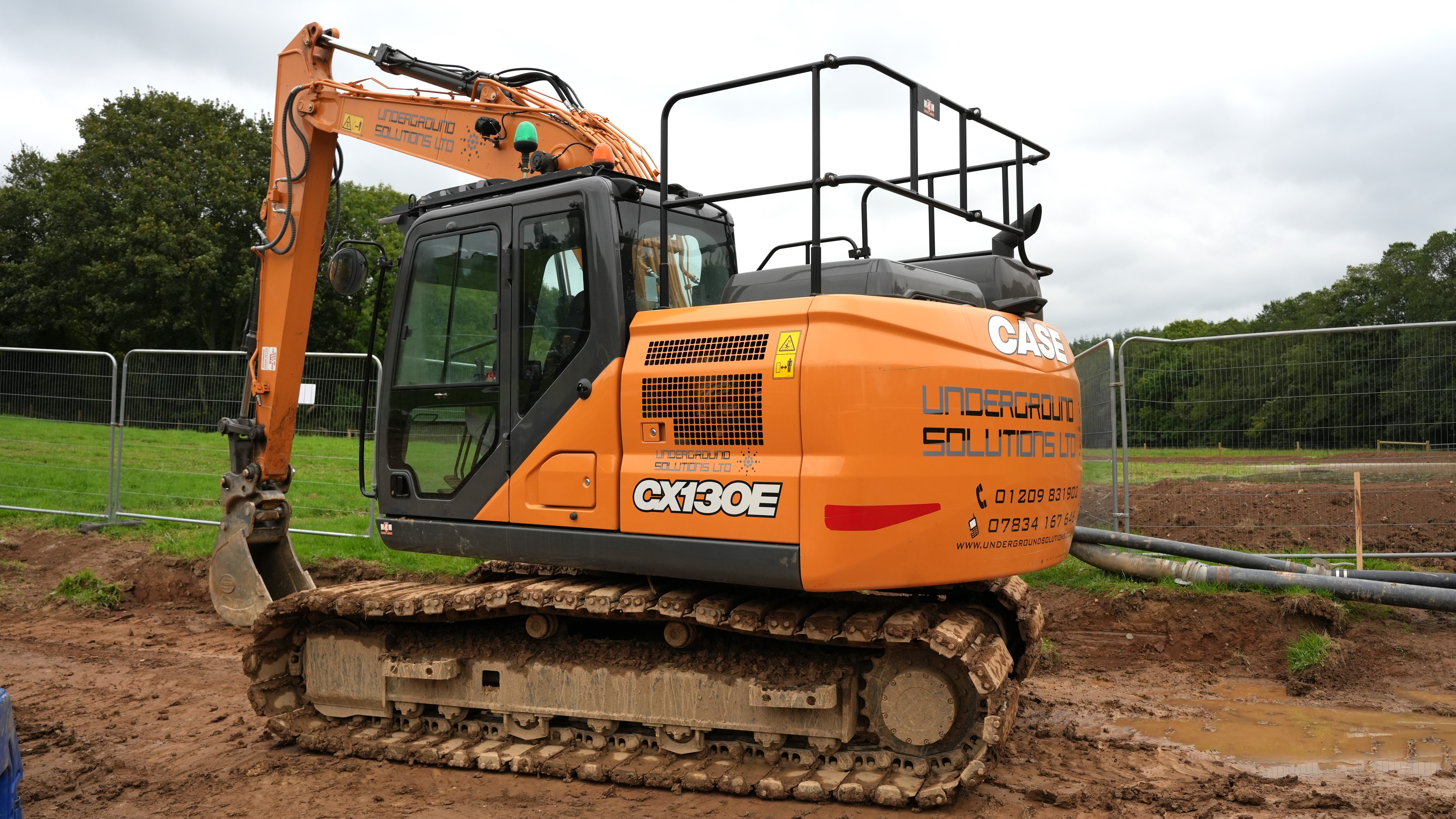
An interesting business that doesn’t just stop there either, as they offer other services including utility location, grab and skip hire and one that really caught my eye on this particular job, directional drilling.
The company has invested in American built Vermeer directional drilling machines, with the first machine being the D23x30, which performs well on smaller jobs, but for hard ground drilling they felt they needed to opt for a larger and more powerful unit, which they now have with the addition of the D40x55 DR (Dual Rod).
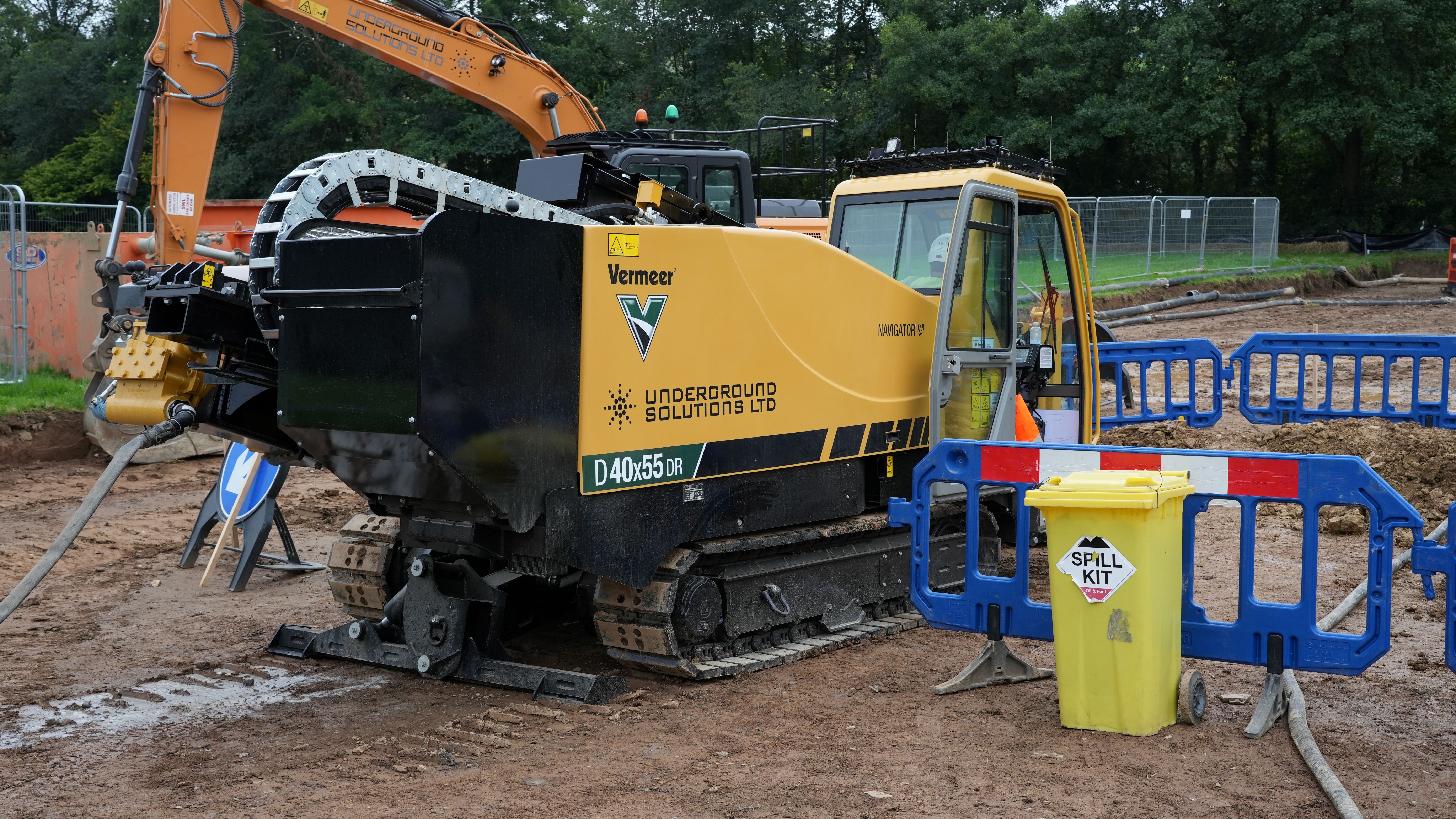
These are not machines that one sees every day, so it was interesting to find out more about them. The drill is powered by an EU Stage V emissions compliant John Deere 4045 diesel engine which produces a power output rating of 140hp @2400rpm. The model numbering denotes the power so its, 40,000 lb (177.9 kN) of thrust/pullback and 5500 ft-lb (7457 Nm) of rotational torque at the drill end, this specific drill is running a 10ft (3m) drill rod running on a 25/8 thread.

With the 20-tonne US, 18-tonne UK, class machine working in dual rod mode, this means that you have a rod inside a rod, so effectively, one rod drives the bit on the end of the drill, while the other rod drives the rotation, thrust and steer. This allows them to drill in rock conditions, in single rod configuration its only suitable for drilling in soil.
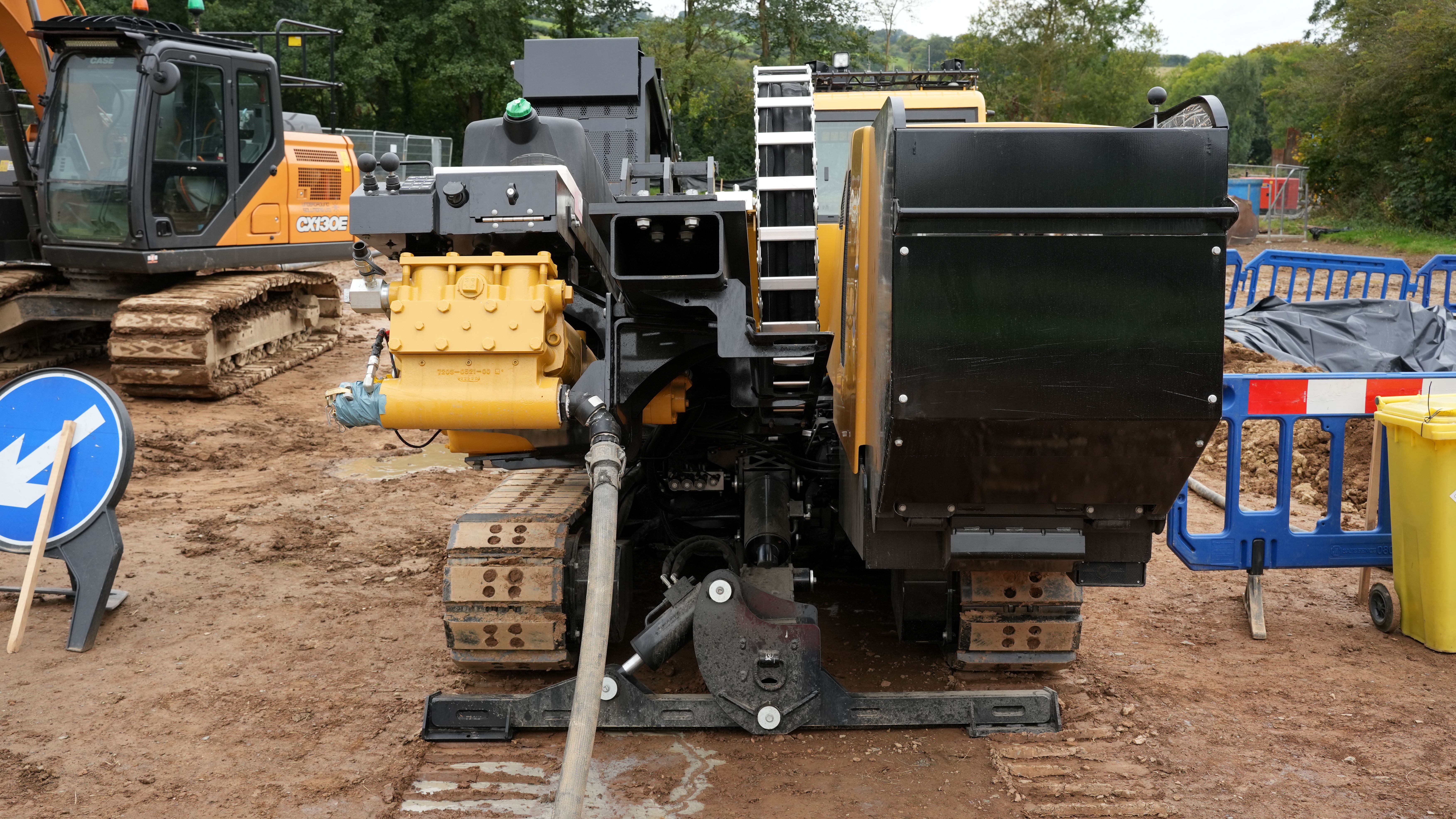
The machine has a 70 gpm (189.3 L/min) Aplex mud pump on board which allows them to be able to fit larger size reams to provide good flow to the drill bit for cutting. When you are drilling down deep and cutting the fluid delivery and the rotational pressure of the drill is what counts. Fluid is delivered at a maximum pressure of 1100psi and the machine itself has an on-board tank capacity of 22.7L. On this job a separate dedicated fluid tank was in use with a much larger capacity.
Specific fluid product additives are used to manipulate the said fluids to do what they want them to do, it’s all very scientific!
On this job in Lifton, Devon, Jamie and his team were undertaking the work for main contractors Kier, drilling a 100-metre shot to install 3 x 180mm electric ducts underneath the river. The specification requires that the ducts have to be installed at 3.7 metres below the river bed itself. From the depth under the river the drill then popped up into the work zone on the other side, where the ducts would be attached and eventually drawn back through.
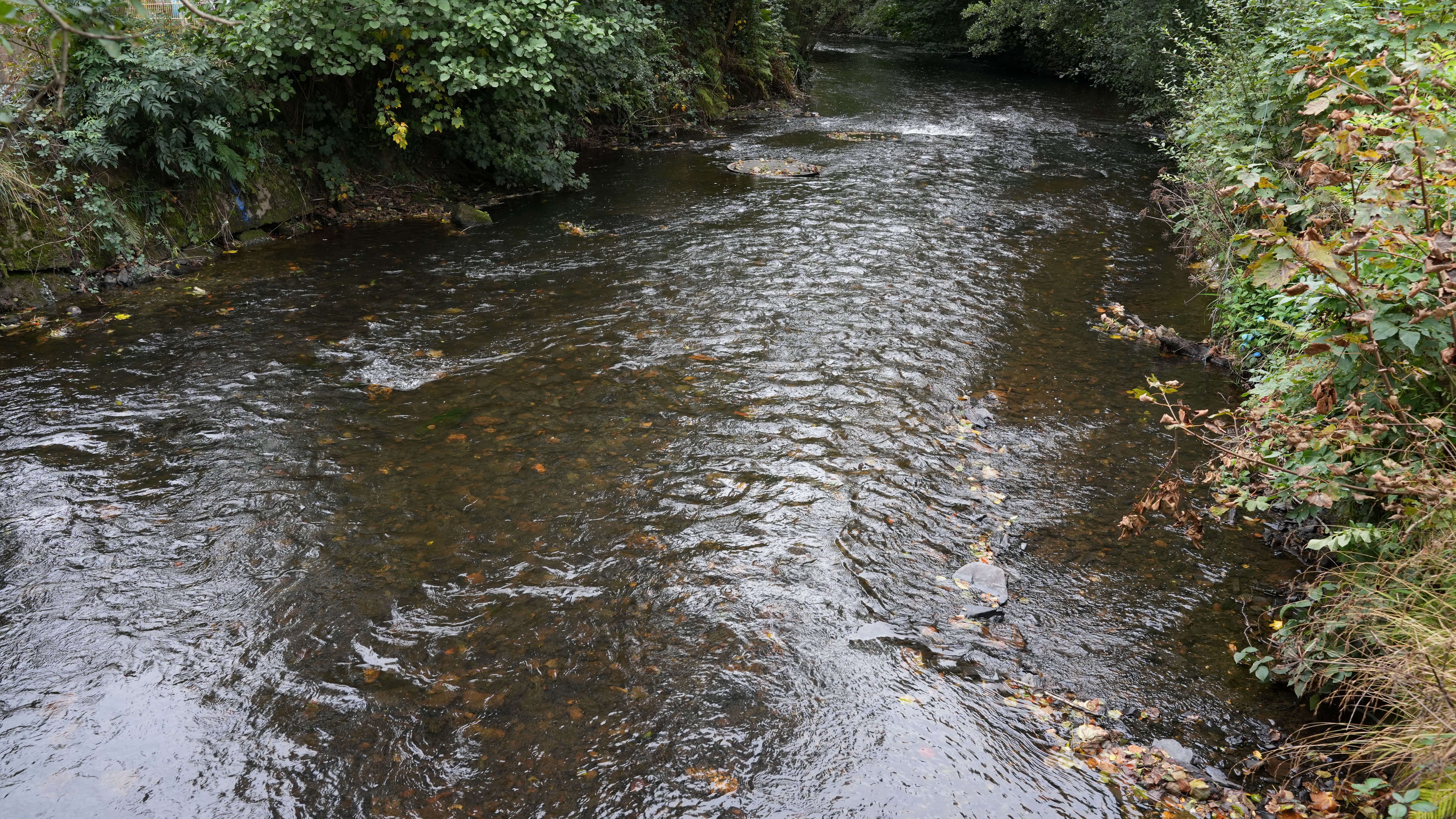
The electric will eventually power a pumping station that will be installed on the site where the drill was stationed, it will be used to pump “raw” water, which will be pumped from another river, up to a local reservoir, where it will be treated and fed back into the main system.
Sat in the cab of the machine viewing the monitors and controls, I asked Jamie for an explanation in layman’s terms of the drilling procedure and how they monitor the course of the operation.
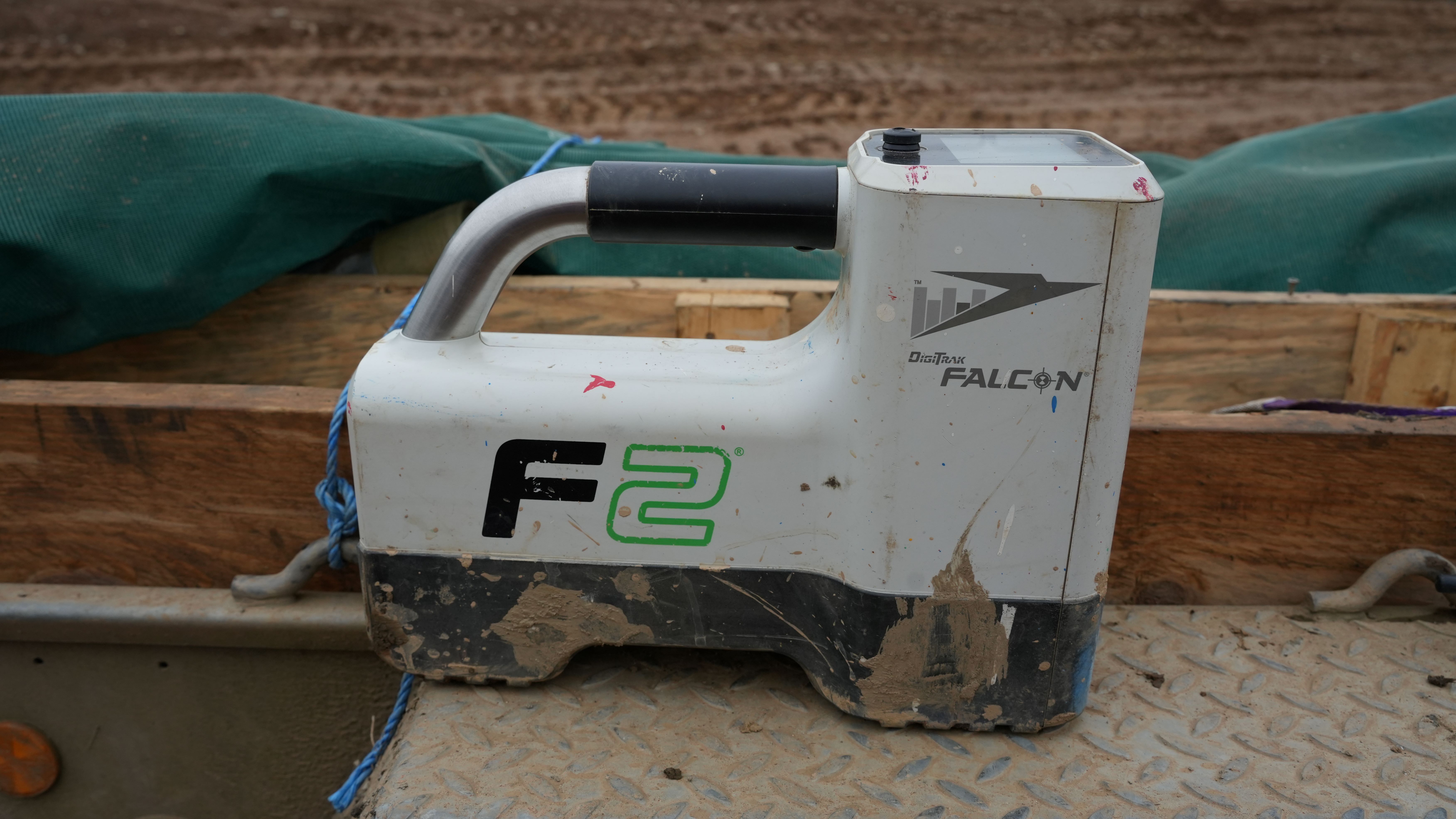
It transpires that a directional drill locating sonde is fitted within the head of the drill, this emits a signal that can be monitored in the cab via a hand-held locating device, in this instance a Digitrak Falcon F2 that sends a whole raft of drill status information back to the drill operator.
This information includes how deep it is, the angle you are head, and most importantly the temperature of the head, this is crucial as an overheating head can be a very costly issue.
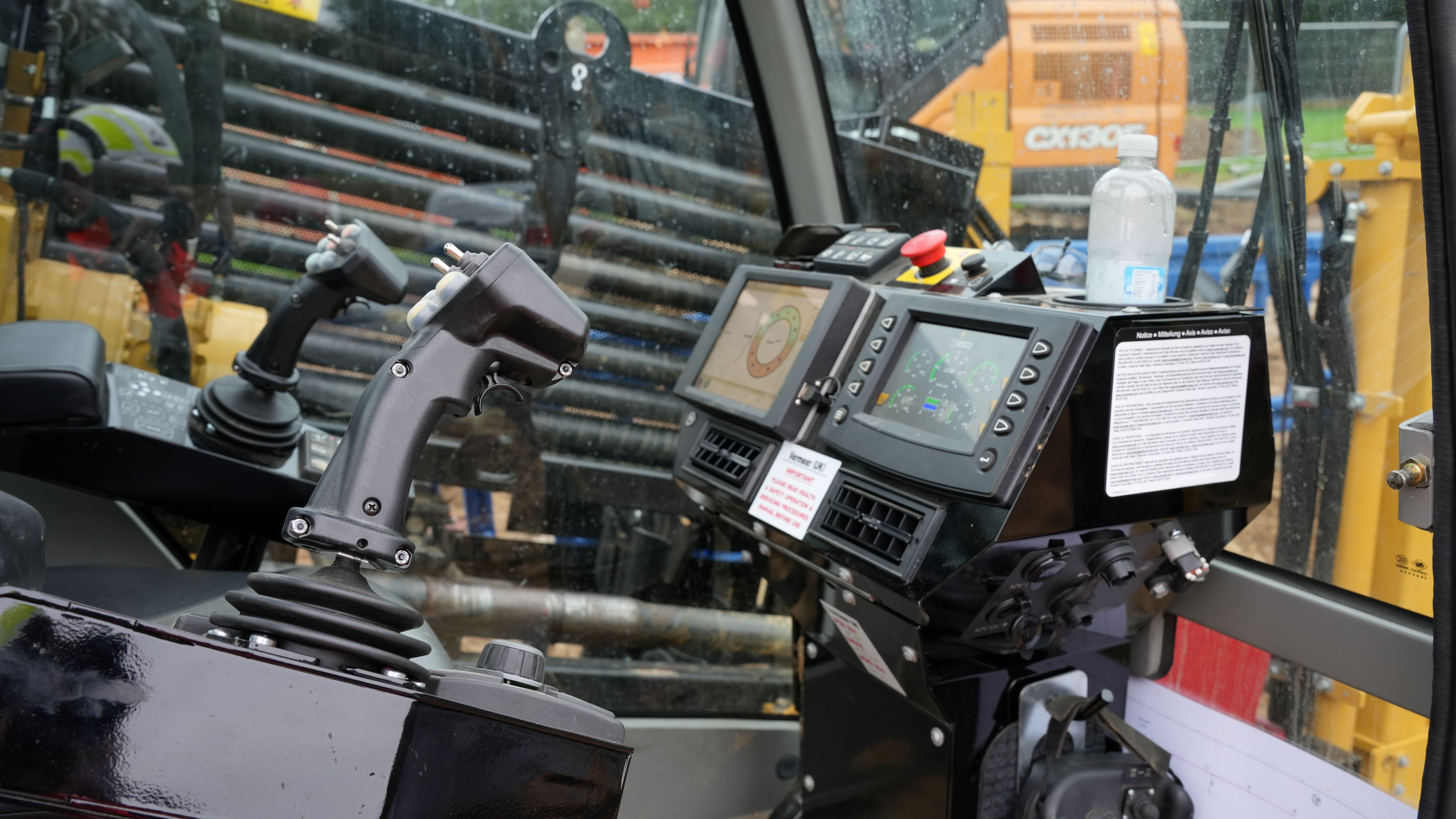
Steering of the drill head is undertaken by the left-hand joystick, the drill head actually has a slight bend in it which facilitates the steering of it. Following the Vermeer Digitrak Aurora screen monitor, the operator works on a clock face scenario. For instance, they work off a 12, 3, 6 and 9 o’clock system in terms of positioning, so if the head was going too deep the tracker will communicate back to the drill operator, put it to 12 o’clock and just give it a little push, in that way the head gets pushed up and back on course, and so on to adjust to suit in whatever position the adjustment is needed.
The cassette style rod storage rack to the operators left, automatically loads the next rod in place as drilling progresses. As a rod drops into place, a set of jaws at the front grab the rod and the operator then turns the gearbox to tighten it, the gearbox then goes back up, and another rod drops into place, and the procedure is repeated.
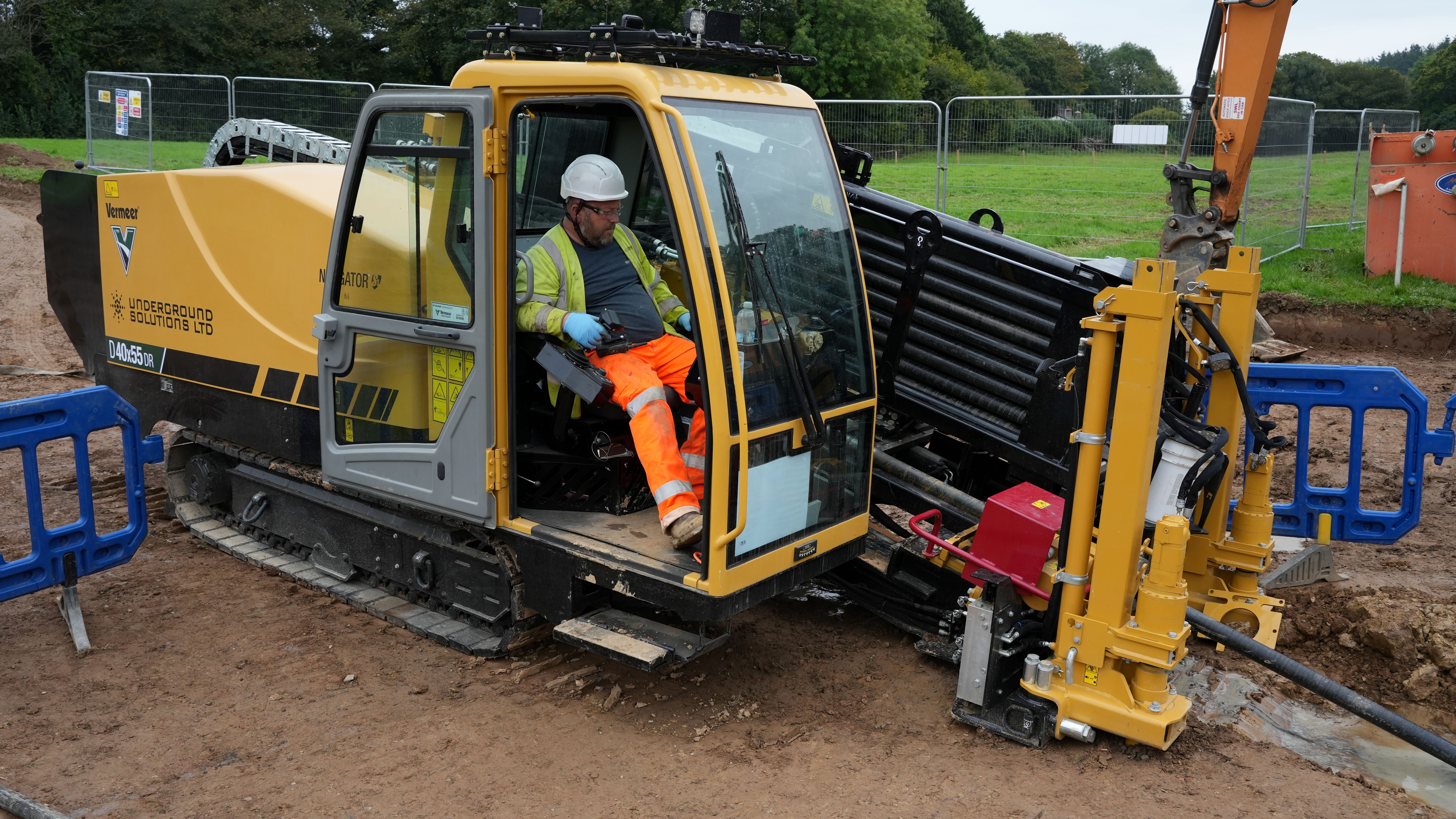
After the initial hole has been drilled the drill head itself is removed and a reamer is fitted which enables you to make the hole bigger, this work is done in stages with different sized reamer heads until you achieve the required diameter, enabling you to pull the pipe back through.
Only certain types of pipe can be pulled back, in this instance its MDPE (Medium Density Polyethylene) which comes in different thicknesses, for this application they are using the middle thickness called SDR11. Using this strength of pipe ensures that it will not stretch during the pull back, something that Jamie explained can easily happen if careful procedures are not followed.
A special towing eye, called a mud tight end, is inserted into the new pipe being drawn back, it is tightened up with a big bar and if done correctly should not come off. As its name suggests the mud tight end does not allow any liquid to run back down the pipe during the operation.
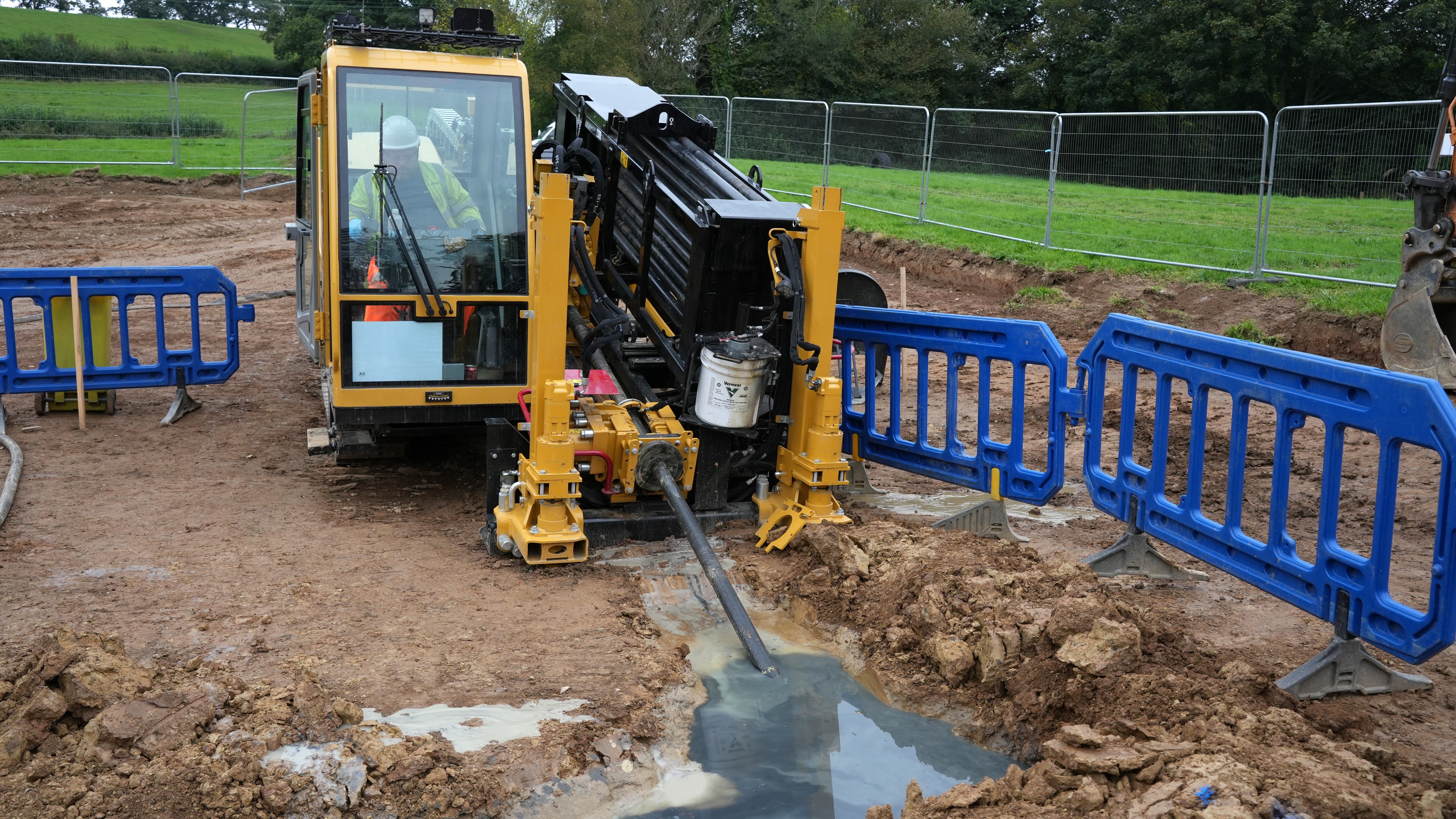
These specialist bits of kit don’t come cheap with the base machine itself costing according to Jamie, somewhere in the region of £600,000 plus all the rods and other accessories.
Talking about the investment Jamie said, “We have had smaller drills for about 4 years now, but before that we noticed that some of our clients were increasingly having drilling work undertaken, and more often than not, they were bringing down companies from up country to do the work, so we thought, well if we haven’t got a drill, we are never going to be asked to do any drilling work, so that was when we took the decision to invest in one and we have never looked back”.
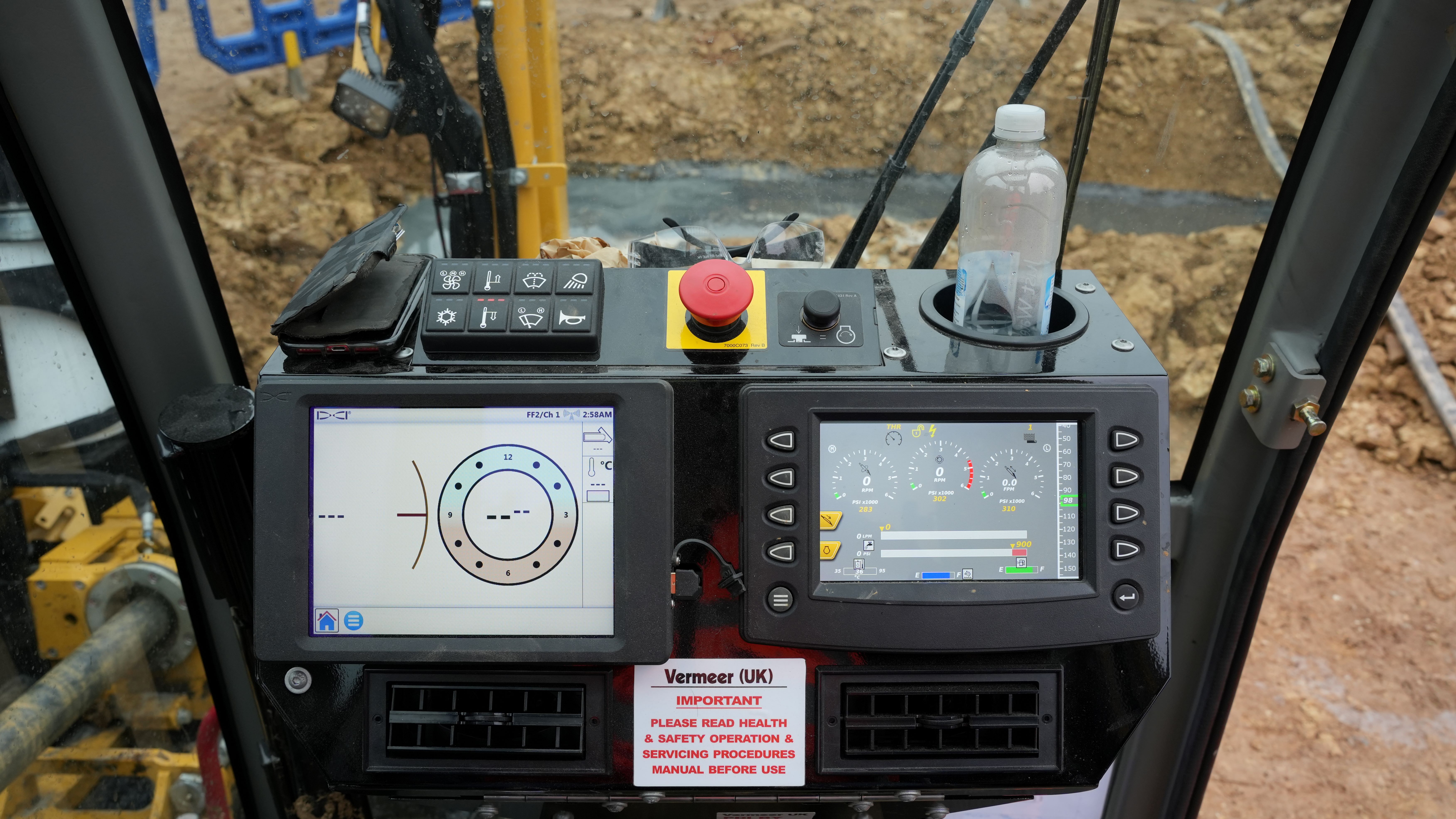
Underground Solutions are certainly making an impact in the South West, especially with their stunning fleet of grey liveried vacuum excavations trucks, which I seem to spot all over the place these days, something we must get out to see for a future article in this magazine for sure.
Vermeer who are based in Pella, Iowa, USA, is still a family-owned business who celebrated 75 years in business last year. Alongside their drilling machines the company also produce a wide range of niche products for various sectors including agriculture, landscaping, recycling, tree care and wood waste industries to name a few.