by Kyle Molyneux | Thu 22 Jul 2021
Berco develops undercarriage for Cat 6020B
Berco, which manufactures and supplies undercarriages and components to OEMs and the Aftermarket, has launched a complete undercarriage replacement range for the Cat 6020B Hydraulic Mining Shovel. Developed specifically for the high-quality demand mining segment of the Aftermarket, this is the first ‘non-captive’ range available to purchase. This means that aside from Cat, Berco is the only company currently capable of providing a full and significantly more affordable variety of undercarriage replacement components for this particular machine.
Launched some years ago, the Cat 6020B is a 230-ton excavator at the very high end of the mining range. Depending on the abrasiveness of the soil, undercarriage components need to be replaced every four to five years. This means that there are significant numbers of this particular model currently due undercarriage maintenance. This number, moreover, is forecast to grow in the coming years. To meet this demand, Berco is supplying a full range of undercarriage components which include the chain, the bottom rollers, the top rollers, the drive sprocket and idlers with supports. Everything is set to be available from September onwards.
For the Cat 6020B Hydraulic Mining Shovel range, the company utilised a ‘reverse engineering’ process to deconstruct the OE components. Three-dimensional material scanning was carried out in order to gain a complete understanding of the initial design criteria, while laboratory analysis determined the materials used as well as the heat treatments and microstructures.
Having gained a full understanding of all of the components in question, company engineers then proceeded to develop their very own Berco-quality Aftermarket undercarriage system, which is further boosted by the addition of another Berco innovation: BPR2 (Berco Positive Pin Retention2 System). This is said to improve the working lifetime of the components by mechanically locking the link to the pin which results in the avoidance of ‘end-play generation’ and ‘pin walking’ in an undercarriage.
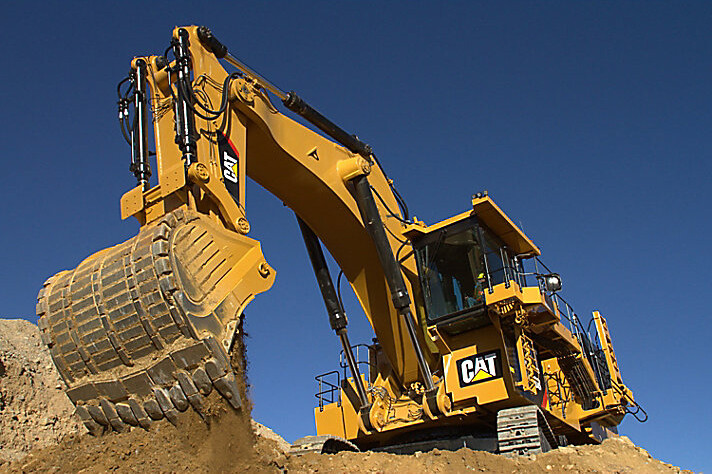
For the track chain, a newly designed track link with a 350mm pitch was produced using the ‘drop forged’ process, made from a mild carbon steel grade with boron. Unlike the OE product, however, the chemical composition of the Berco version is enriched with chromium (Cr) to increase tensile resistance. In addition, the track bushing has a high resistance to wear. With 60 HRC hardness, it can contain pitch elongation. In addition, the case depth has been increased by 20 to 25% when compared to the original. The track pin, moreover, has deeper case depth and higher core hardiness, resulting in an improved bending load resistance.
The track roller can, as a result of its lubrication and seal features, adopt an ‘all-weather’ configuration, ranging from -40C to +50C. Additionally, three top rollers without a central flange support the heavy weight of the chain and the oil filling hole has been moved to the outer collar in order to ensure full access to it.
With the Berco’s Dozer Line already complete, the launch of its range for the Cat 6020B Hydraulic Mining Shovel brings the company closer to finishing its Excavator Line too. For Berco, this is another large step on the way to becoming an overall solution provider for the Aftermarket.
Accounting for a big portion of all Aftermarket sales, the mining market segment is of particular importance to Berco. The company is now looking to further strengthen its position there by extending its mining ranges and becoming the only high-quality alternative to the OEMs.
Got a news story? Email news@earthmoversmagazine.co.uk.
