by Kyle Molyneux | Mon 30 Nov 2020
Extreme jobs for MB Crusher kit
MB Crusher, an Italian designer and manufacturer of crusher buckets, has highlighted some of its customers’ most memorable jobs in 2020 involving its products. For one application (pictured above), a BF60.1 MB mobile crusher was disassembled and carried in parts by helicopter to a lodge 6,000ft above sea level in the Bavarian Alps. Upon its arrival, the crusher was rebuilt and got to work chewing up material from the lodge’s demolition. Traditionally, the demo waste material would’ve been hauled downstream and discarded, but this process saved large sums of money on waste disposal and hauling fees.
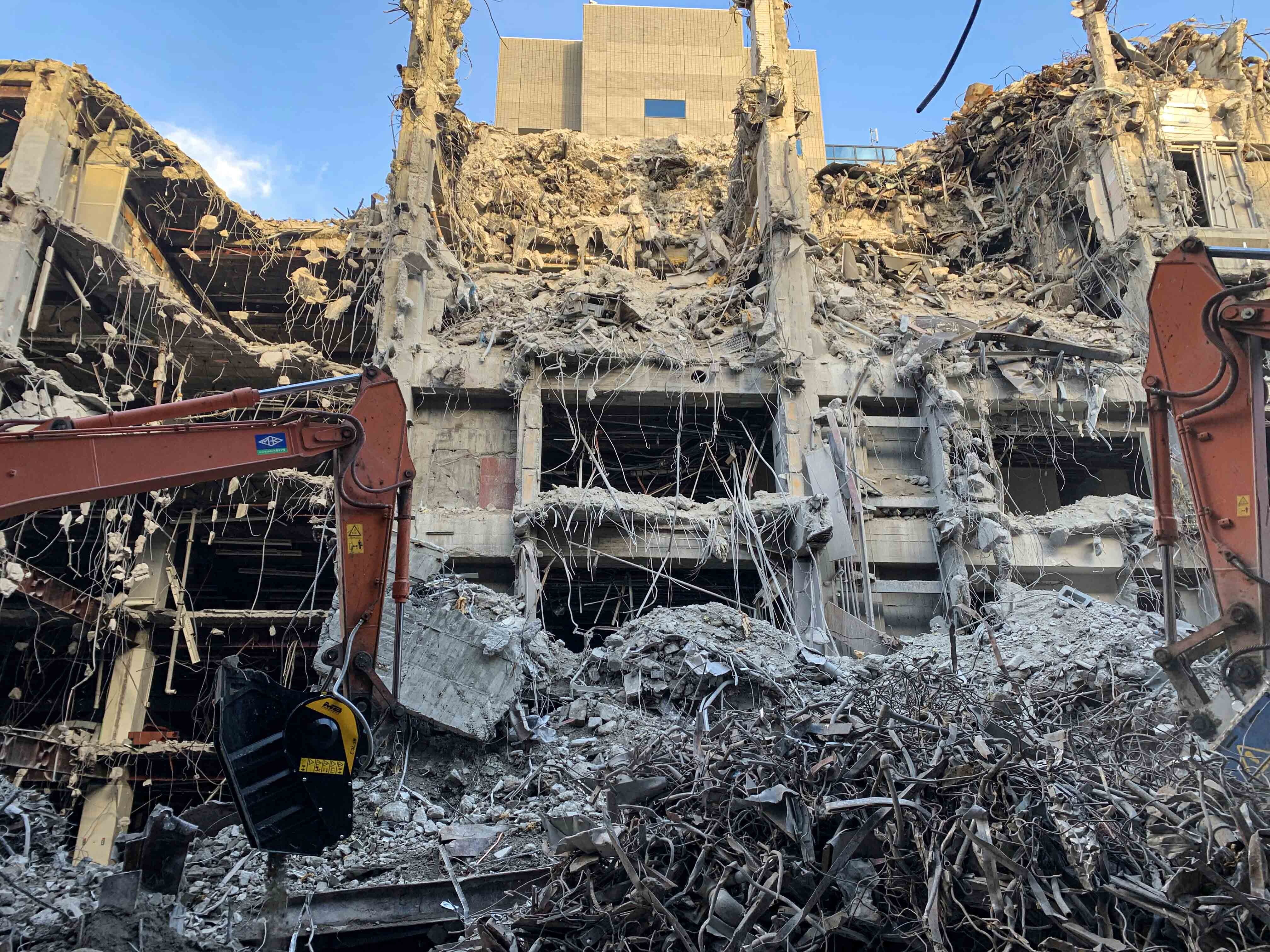
On another demolition job, this time in the centre of a large Japanese city (shown above), a BF70.2 MB mobile crusher was chosen for its ability to process reinforced concrete in narrow spaces. The crusher bucket was lifted to the 16th floor of a reinforced concrete building, surrounded by other properties and city life, with a crane.
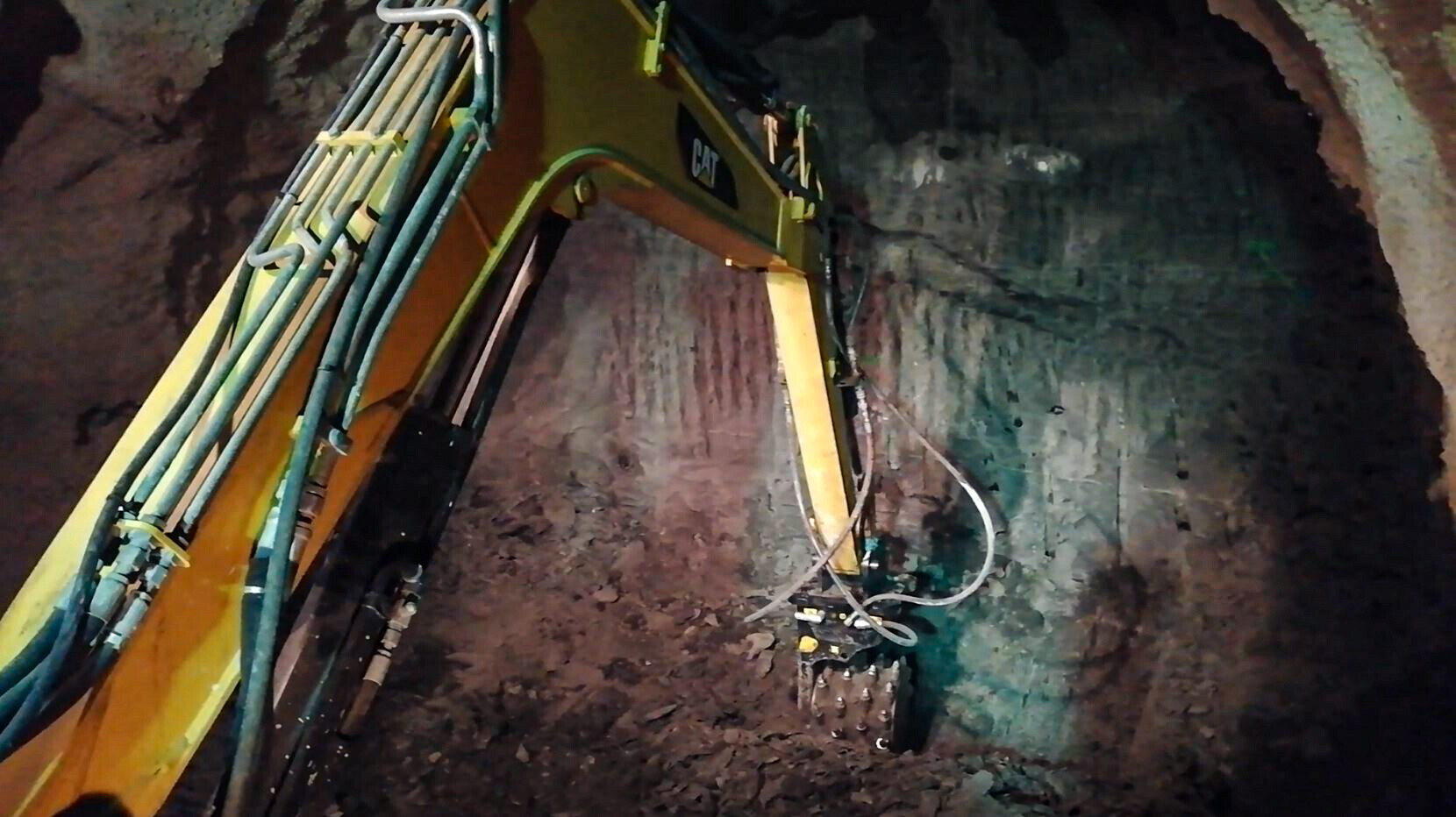
Contrast that application with the one in Southern California, where an MB-R500 drum cutter was used to dig an underground drainage canal (see picture above). The aim was to avoid flooding a busy road above, but the difficulty lay in the tunnel’s narrow profile which was inaccessible by regular machines. Furthermore, a hammer would’ve caused excessive vibrations and cracks in the wall.
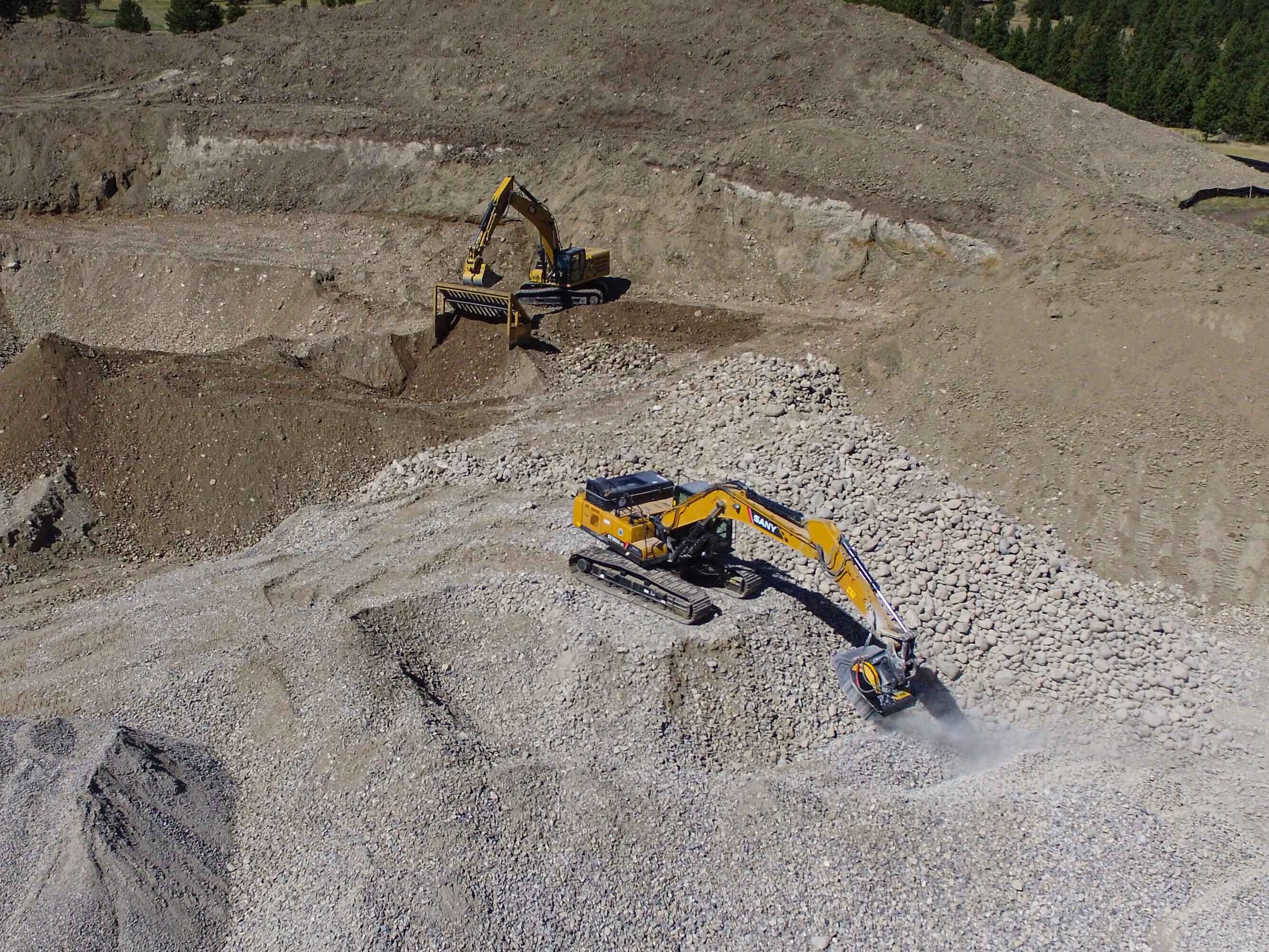
Further north, in Montana, USA, a contractor had the task of preparing the site of a new residential area (above). During the excavation phase the company ran in to large amounts of river rock, do deployed a BF120.4 mobile crusher to break down river rock for immediate reuse as fill. This saved haulage and material handling fees while eliminating buyback expenses. The company estimated tens of thousands of dollars of savings.
Got a news story? Email news@earthmoversmagazine.co.uk.